在我们常见的塑胶制品中已经很难再见到塑胶起皮的现象了,在十年前吧,我们很容易买到洗脸的塑料脸盆上会起皮.起皮随事小,但是最直接的是影响美观,今天我们就来谈谈塑胶起皮现象!
常见的起皮材料主要为PC塑料以及ABS塑料的融合体,这种融合体主要用在汽车的内部装饰中,电器的外壳中最为常见.
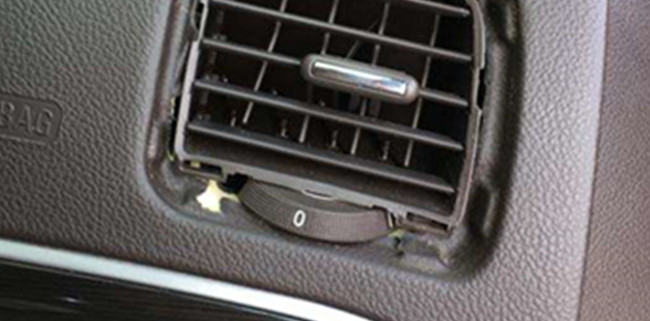
纵观塑胶制品起皮现象的三大原因
1:在注塑加工时塑料受到污染引起
当塑料受到污染时,这个非常简单,ABS塑料以及PC塑料相融不够充分,中间隔着污染源,导致ABS塑料以及PC塑料产生分层现象,最终导致塑胶起皮现象.
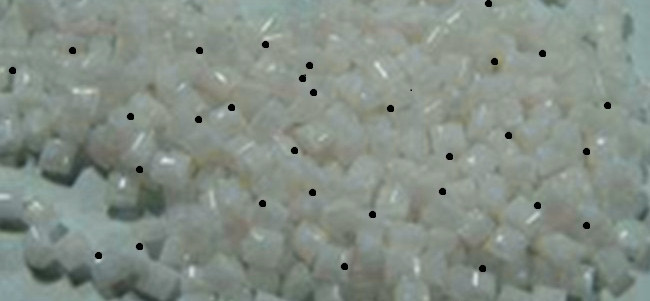
2:在注塑加工时模具设计不当引起
在注塑加工的时候如果发现模具设计不当,外壳壁过薄,在ABS塑料和PC塑料在充分融合的情况下,如果设计过分薄,塑胶外壳也可能出现分层现象,最终导致塑胶起皮现象.
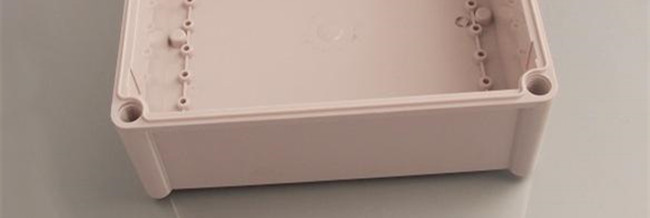
3:在注塑加工时注塑工艺达不到要求引起
如果工艺不成熟时,出现高的高剪切下发生流体的破裂及两相的分离,继而产生分层起皮现象。
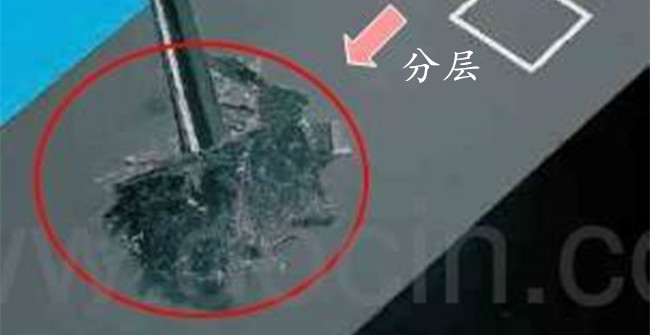
关于流体破裂进行重点说明一下
起皮的主要原因无非是在注塑加工的时候引起,这个也无可厚非,当塑胶制品已经成型,起皮现在就很少发生,除非是塑料的质量太差引起,否者不会出现成型后再次起皮现象.下面我们来分析一下原因
塑胶起皮的终究原因是熔体破裂,破裂之后就会出现我们看到的脾气现象,那到底为什么会有熔体破裂呢?
当PC塑料与ABS塑料聚合后,生成聚合物,这种塑胶杯挤出进行注塑成型,或者我们可以说被射出注塑成型前,这时候经过口模和浇口挤出来的聚合物塑胶它有着光滑的外表,同时拥有者均匀的形状,这个时候的流体剪切是比较正常的.
当流体剪力增加时,这时候同时剪切应力也增加,当他们俩增加到一定要求值的时候,这时候挤出来的塑胶会出现不良反应,挤出物表面失去光泽,我们用手抚摸塑胶外壳表面时会感觉到粗糙.
当流体剪力再增加时,挤出物挤出的速率再升高,这时候挤出物塑胶制品表面会出现众多的不规则的结点,有时候会出现扭曲的现象,有时候也会有竹节纹的现象,最最不敢想象的是出现断裂,支离.这样的结果是使塑胶裂成碎片,柱段,这时候出现的塑胶零界点,我们称之为熔体破裂.
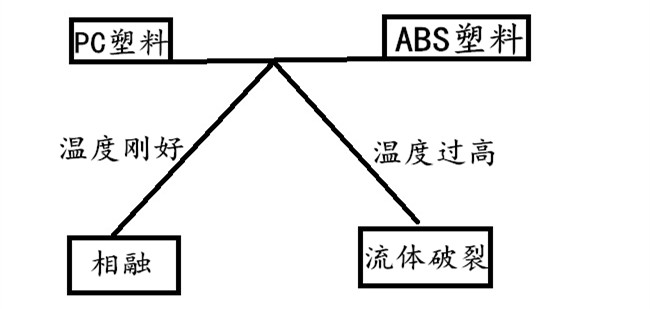
根据以上三点,我们可以得出一些结论
1:剪切应力低下时,塑料颗粒会发生小的扰动,这种小的扰动在注塑制品后影响不大
2:当剪切应力发生变化时,当他们变大时,塑料颗粒的不稳定性增加,可以看出ABS塑料和PC塑料融合体随着温度的升高不稳定性,不确定性升高.
3:当剪切应力升高到一定程度的时候,会达到零界点,会引起流体的破裂
总结
产生起皮的重要原因:PC塑料与ABS塑料之间只能部分相融,随着温度升高,相融度变高,达到一定温度后,相融度变低,达到一定零界点后,产生熔点破裂.
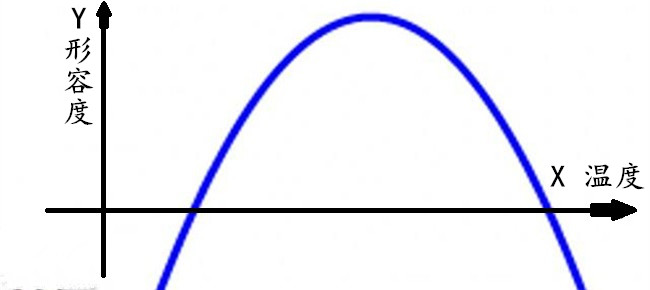
针对塑胶起皮的解决方法
1:在PC塑料和ABS塑料中加入适当的相容剂提高相容性.
2:温度控制方面,需要达到ABS塑料与PC塑料融合的最适宜温度下进行注塑加工.
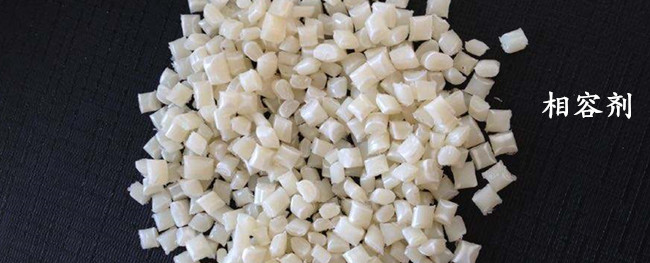
